UNDERSTANDING CORROSION IN AND AROUND YOUR BOAT
Corrosion is a concern for many boaters. Corrosion damage is often unsightly, unsafe and costly.
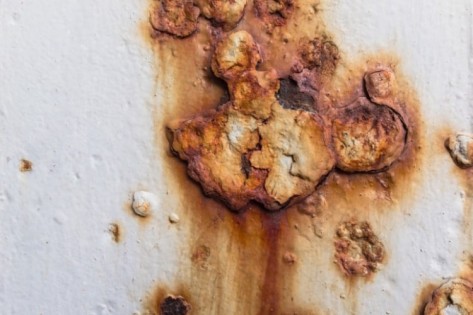
It is possible to rise to the challenge posed by various sources of corrosion. As Mercury Marine says, “Marine corrosion is a fact of boating life, but you can protect your investment with diligence & proper maintenance.”
Certain kinds of corrosion can devalue your investment in a matter of months or even days. Many boating enthusiasts do not know what specific threats to look out for. Let’s shine some light on the topic.
TYPES OF CORROSION
An article in Seaworthy discusses types of corrosion that boaters combat, including simple, electrolytic, crevice and galvanic.
SIMPLE
Simple corrosion occurs when molecules on a metal surface bond with oxygen. The process is called oxidation. Moisture accelerates the chemical reaction. In marine applications, aluminum deteriorates into aluminum oxide, a grayish substance.
Fortunately, stainless steel and other coatings prevent oxidation. Simple corrosion in a marine setting is often very gradual. For example, simple corrosion of a bronze propeller occurs at a slow rate. So slow, in fact, that the process may not impact service life.
ELECTROLYTIC
In marine settings, stray electrical current quickly accelerates corrosion. Electrical shorts are often the culprit. Many of them occur in the 12-volt battery systems common on boats. When there’s a short, electrical current may flow through an underwater metal fitting. The resulting electrolytic corrosion can do serious damage in days or hours. Regular boat inspections and prompt diagnosis address the threat posed by electrolytic corrosion.
CREVICE
Crevice corrosion is a threat to stainless steel used in marine environments. The “stainless” nature of the metal is due to its oxidised surface. Here, oxidation is actually beneficial, inhibiting corrosion. When moisture combines with a shortage of oxygen, problems arise. Unwanted leaks may lead to crevice corrosion in bolts and fittings.
GALVANIC
Galvanic corrosion is a significant concern in marine environments. Different metals immersed in water essentially become a battery. A metal with more negatively charged ions acts as the anode. Ions flow to the less negatively charged metal – the cathode. The greater the difference in voltage between the two, the more rapid the loss of anode material. Galvanic corrosion is the result.
In a marine environment, serious galvanic corrosion can happen in months. Fortunately, the proper use of sacrificial anodes controls the process.
Sacrificial anodes – A sacrificial anode contains a metal lower on the galvanic table than the other metals on the boat. It takes the corrosive threat away from metal hulls and stern drives.
In many systems, different metals are bonded together into a single cathode using 8 AWG green insulated wire (ABYC Standard E-2). It’s important to check the boat’s sacrificial anodes on a regular basis.
Three metals are popular in sacrificial anodes. Aluminum anodes are often used in boats used in both freshwater and saltwater. Magnesium anodes are appropriate for freshwater applications. In the past, zinc anodes were common. However, freshwater causes a coating of zinc oxide that limits effectiveness.
Supplementary systems – Sacrificial anodes are not always enough. Sometimes, the area that needs protection is too large. Or, the voltage difference between the anode and the cathode is insufficient.
As a result, it is often important to add a supplemental system. A sensor delivers real-time data, signaling the system to increase the electrical current to protect connected metals. Mercury Marine’s MerCathode system is an example of a supplemental system.
PERIODIC INSPECTIONS AND MAINTENANCE
Professional inspections and prompt maintenance help you guard against corrosive damage. To protect against electrolytic corrosion, make sure your boat’s electrical system is in good working order. Reduce the potential for electrical shorts with a well-maintained battery system. Counter the threat of galvanic corrosion with sacrificial anodes and supplementary systems. Ensure they work according to spec.